Injection Mold Tool Design: A Comprehensive Guide
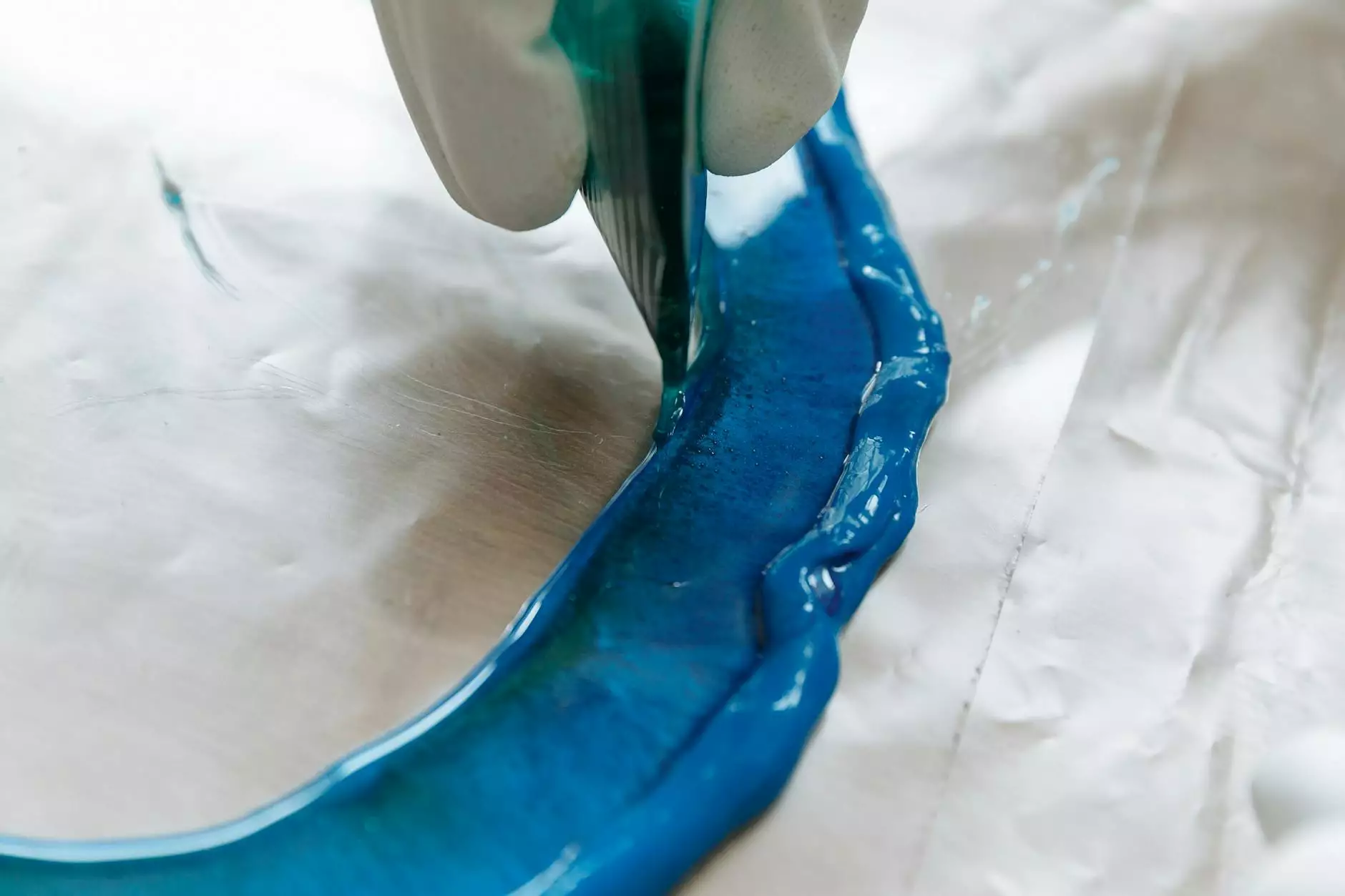
Injection mold tool design is a critical component of the manufacturing industry, particularly in the production of plastic components. With the rise of technological innovations and the growing demand for efficiency and precision, businesses are turning to sophisticated mold design methods to enhance productivity and maintain competitive advantages. This article explores the fundamentals of injection mold tool design, its various elements, and the exceptional services provided by deepmould.net in the realm of metal fabrication.
What is Injection Mold Tool Design?
At its core, injection mold tool design refers to the process of creating molds used for shaping molten materials, primarily plastics, into specific forms. This design phase includes the consideration of factors like material choice, mold geometry, cooling systems, and ejector mechanisms, all of which contribute to the efficiency and quality of the final product. High-quality injection molds are essential for mass production, enabling consistent results over numerous production cycles.
The Importance of Injection Mold Tool Design
Effective injection mold tool design serves several vital functions in the manufacturing process, including:
- Precision: Accurate mold design ensures that the produced parts fit perfectly and meet stringent specifications.
- Cost Efficiency: Designing molds with optimized cycles reduces material waste and lowers production costs.
- Durability: Well-designed molds can last for thousands of cycles, minimizing the need for replacements.
- Consistency: High-quality molds yield consistent results, essential for maintaining product quality across larger batches.
Key Elements of Injection Mold Tool Design
The process of injection mold tool design encompasses several elements that directly impact the mold's functionality and the quality of the final product. Key elements include:
1. Mold Material Selection
The choice of material for the mold itself is critical. Common materials used include:
- Steel: Durable and suitable for high-volume production.
- Aluminum: Lightweight and offers quicker turnaround times for lower volume production.
- Composites: Provide balance between weight and durability.
2. Mold Design Geometry
Mold geometry refers to the shapes and features designed into the mold. This includes considerations for:
- Cavity design: The negative shape that defines the parts.
- Core and cavity fit: Ensuring precise alignment for effective release of the molded part.
- Draft angles: Slight inclinations that facilitate the easy removal of molded parts.
3. Cooling System Design
Effective heat management is crucial for maintaining the quality and speed of the production process. The cooling system design must consider:
- Cooling channels: Strategically placed channels that help regulate the temperature of the mold.
- Heat transfer materials: Materials that enhance the cooling process effectiveness.
4. Ejection Mechanism
The ejection mechanism is essential for removing the part from the mold after it has cooled. Common types include:
- Mechanical ejectors: Use a pin or plate to push the part out.
- Hydraulic ejectors: Utilize hydraulic pressure for removal, ideal for complex shapes.
5. Safety Features
Incorporating safety features in mold design prevents accidents during operation. Important considerations are:
- Emergency stops: Allows for immediate cessation of the injection process.
- Safety interlocks: Prevents operation under unsafe conditions.
Technology and Innovation in Injection Mold Tool Design
With advancements in technology, injection mold tool design continues to evolve. Innovations are transforming how molds are designed, produced, and used:
1. Computer-Aided Design (CAD)
CAD software allows designers to create detailed 3D models of molds, making it easier to visualize and modify designs before production. This technology significantly reduces errors and improves efficiency in the design process.
2. 3D Printing
3D printing technology allows for the rapid prototyping of molds. Designers can quickly create models to assess functionality, fit, and aesthetics before going into mass production, ultimately saving time and resources.
3. Simulation Software
With the use of simulation software, manufacturers can predict how the molten plastic will flow within the mold. This helps in identifying potential issues, optimizing the design, and ensuring high quality in production.
Benefits of Partnering with Deepmould.net
For companies looking to enhance their injection mold tool design process, partnering with a leader in the metal fabrication industry like deepmould.net provides numerous advantages:
- Expertise: Deepmould.net has extensive experience and knowledge in mold design and fabrication, ensuring high-quality results.
- Customer-Centric Approach: Their team collaborates closely with clients to understand unique requirements and deliver tailored solutions.
- Advanced Technology: Utilization of the latest technologies in CAD, simulation, and 3D printing expedites the design process while enhancing quality.
- Quality Assurance: With stringent quality control measures in place, clients can trust in the durability and performance of the molds produced.
Conclusion
In conclusion, injection mold tool design is a vital aspect of the manufacturing process that significantly influences product quality and production efficiency. Understanding its intricacies, from material selection to technological advancements, empowers businesses to make informed decisions and optimize their manufacturing operations. By collaborating with leading experts like deepmould.net, companies can leverage advanced design capabilities and innovative solutions to stay ahead in a competitive marketplace.
Frequently Asked Questions (FAQ)
1. What industries benefit from injection mold tool design?
Many industries, including automotive, consumer goods, medical devices, and electronics, utilize injection mold tool design for producing high-quality plastic and metal components.
2. How long does it take to design and produce an injection mold?
The timeline can vary based on complexity, but typically, the design and production of an injection mold can take anywhere from several weeks to a few months.
3. What is the average lifespan of an injection mold?
With proper maintenance, the lifespan of an injection mold can range from thousands to millions of production cycles, depending on the material used and the complexity of the design.
4. Can I get custom molds designed?
Yes, companies like deepmould.net offer custom injection mold tool design services tailored to meet specific requirements and applications of clients.