Exploring the Benefits of Silicone Compression in Business
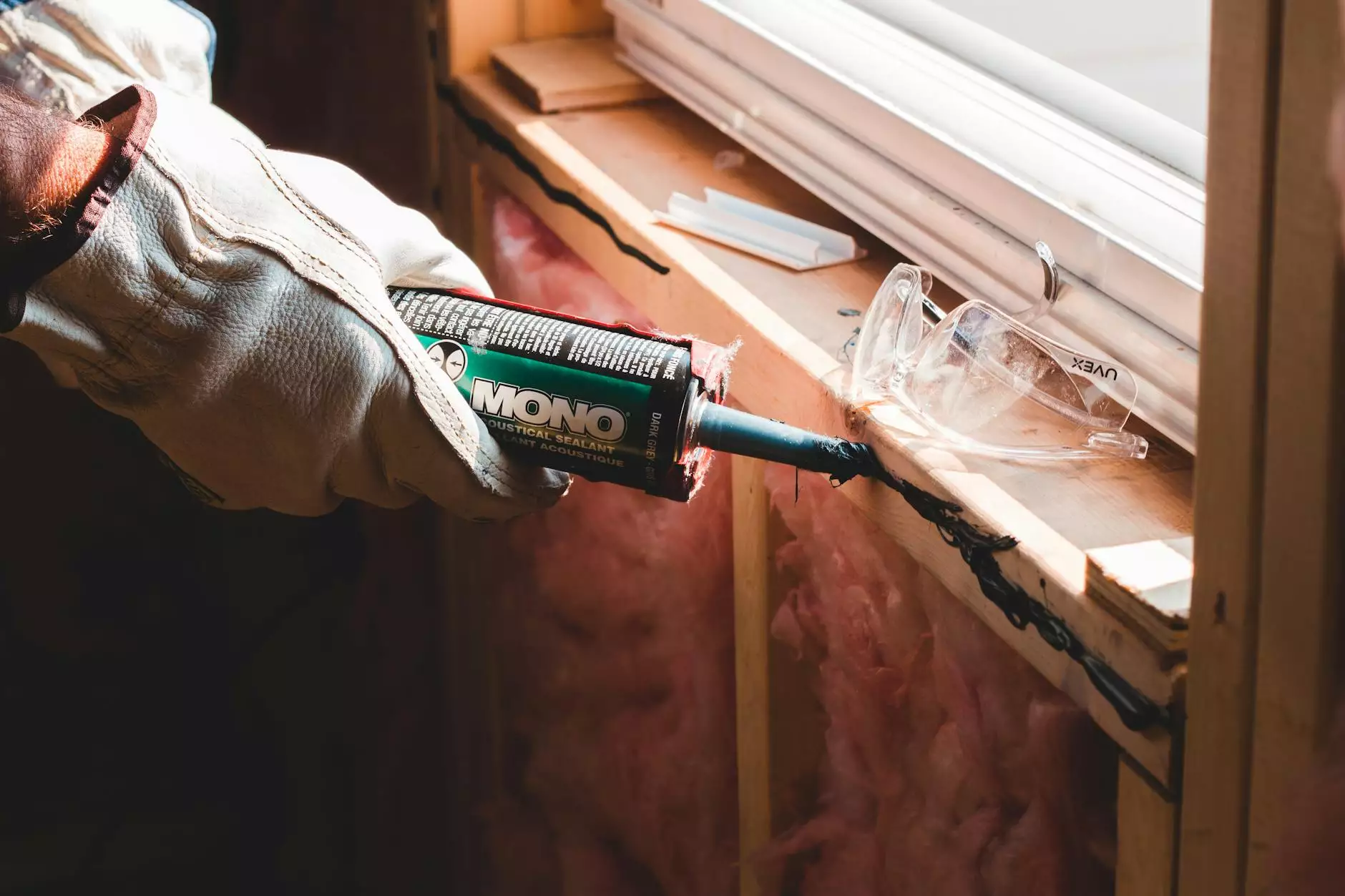
Silicone compression has emerged as a significant component in various industries, especially in electronics and medical supplies. The versatility, durability, and adaptability of silicone materials make them ideal for a range of applications. This article delves deep into the various aspects of silicone compression, its benefits, applications, and its influence on modern business practices.
Understanding Silicone Compression
Silicone compression refers to the process of using silicone rubber that can withstand significant compression while maintaining its integrity. This property allows silicone components to be molded into various shapes and sizes, capable of withstanding wear and tear, extreme temperatures, and exposure to chemicals. The molecular structure of silicone gives it unique properties that contribute greatly to its application in high-performance environments.
Key Properties of Silicone
To appreciate the advantages of silicone compression, it is essential to understand what makes silicone a superb choice:
- Durability: Silicone materials are highly resistant to degradation, maintaining performance over extended periods.
- Temperature Resistance: Silicone can operate effectively in a wide range of temperatures, from -60°C to +200°C (-76°F to +392°F).
- Chemical Resistance: It is resistant to various chemicals, making it suitable for medical and industrial applications.
- Flexibility: Silicone compression allows for flexibility in design and function, which can be tailored to specific needs.
- Non-Toxic: Medical-grade silicone is safe for use in healthcare applications, making it a preferred choice in the medical supplies sector.
Applications of Silicone Compression in Electronics
The electronics industry has widely adopted silicone compression due to its numerous benefits:
1. Sealing and Gasketing
Silicone compression is ideal for creating seals and gaskets that prevent moisture and dust ingress. This property enhances the longevity of electronic devices by protecting sensitive components from environmental factors.
2. Vibration Dampening
Electronic components often undergo vibrations during operation, which can lead to failure. Silicone's natural dampening capabilities allow it to absorb vibrations, reducing wear on critical parts and prolonging the lifespan of devices.
3. Insulation
Silicone can also serve as an insulator in electronic applications, offering resistance to high voltages. This makes silicone components crucial in the manufacturing of circuit boards and connectors.
4. Molding & Encapsulation
Silicone compression molding is used to encase delicate electronic components, providing enhanced durability against impacts and environmental factors. Encapsulation also aids in thermal management and electrical insulation.
The Role of Silicone Compression in Medical Supplies
In the medical field, the properties of silicone lend themselves to numerous critical applications:
1. Medical Devices
Many medical devices incorporate silicone compression for its biocompatibility and ability to be sterilized without compromising integrity. This includes items like catheters, syringes, and valves.
2. Prosthetics and Orthotics
Silicone-silicone compression is used in the production of prosthetics, providing comfort and support. The material's conforming nature makes it ideal for applications that require a close fit against the skin.
3. Drug Delivery Systems
Silicone materials are increasingly utilized in drug delivery systems, including implants and patches. Their controlled release properties make them valuable in chronic treatment plans.
Benefits of Using Silicone Compression in Business
Implementing silicone compression technology in business processes offers several notable advantages:
1. Cost-Effectiveness
While the initial investment in silicone components may be higher than traditional materials, the durability and longevity can lead to substantial cost savings in the long run. Reduced replacements and maintenance mean a lower total cost of ownership.
2. Enhanced Product Performance
Products designed with silicone compression can outperform competitors in terms of durability, reliability, and customer satisfaction. This can lead to increased brand loyalty and market share.
3. Innovation and Customization
Silicone allows for innovative designs that can be customized for specific applications. This flexibility enables businesses to create unique products that stand out in a competitive market.
4. Improved Safety
In medical applications, silicone's non-toxic and hypoallergenic nature enhances patient safety. Ensuring the safety of products can mitigate liability risks and improve brand reputation.
Future Trends in Silicone Compression
As industries evolve, the demand for advanced materials like silicone is expected to grow. Some trends to watch include:
- Smart Technology Integration: As the Internet of Things (IoT) grows, integrating silicone components with smart technologies will enhance functionality in electronics.
- Sustainable Practices: The push for sustainability will drive the development of eco-friendly silicone materials for greener medical and electronic applications.
- Advanced Manufacturing Techniques: Progress in manufacturing methods, such as 3D printing using silicone, will open new avenues for customization and application.
Conclusion
In summary, silicone compression is a vital aspect of modern business in the electronics and medical supplies sectors. The unique properties of silicone materials offer significant benefits, including improved durability, temperature and chemical resistance, and the ability to create innovative and customizable products. As industries continue to evolve, the role of silicone will only become more prominent, pushing boundaries and setting new standards in product performance and safety.
Companies like nolato.com are leading the way in harnessing the potential of silicone compression, driving innovation and providing high-quality solutions to meet the growing demands of the marketplace. By adopting silicone technologies, businesses can ensure they remain competitive in an increasingly complex and fast-paced world.