Understanding GRP Composite Housings: Advantages, Applications, and Innovations
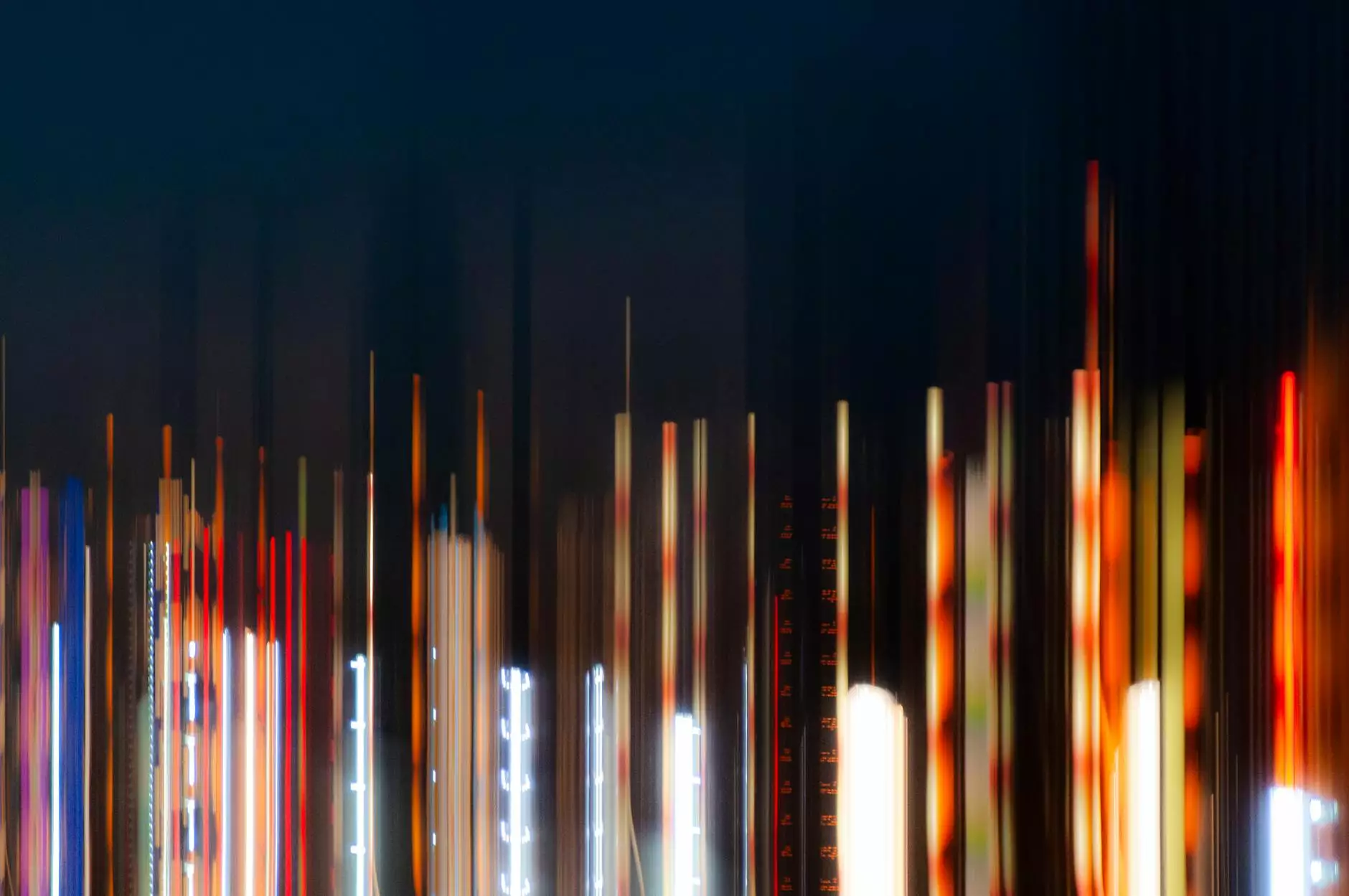
In the contemporary industrial landscape, GRP composite housings have emerged as a vital solution for various sectors requiring durability, reliability, and performance under challenging conditions. This article delves deep into the essence of GRP composite housings, illustrating their benefits, applications, and innovative features that make them stand out in the marketplace.
What is GRP?
GRP stands for Glass Reinforced Plastic, a composite material made by combining a polymer matrix with glass fibers for reinforcement. This fusion creates a material that boasts exceptional strength, lightweight properties, and corrosion resistance.
The Composition of GRP Composite Housings
Understanding the composition of GRP composite housings is crucial to appreciating their benefits:
- Matrix Material: Typically, the matrix is a thermosetting resin, most commonly epoxy, polyester, or vinylester, which binds the glass fibers together.
- Reinforcement: The glass fibers are what give GRP its strength and rigidity, enabling it to withstand various stressors in demanding environments.
- Additives: Depending on specific applications, additives may be included to enhance properties such as UV resistance, flame retardance, or conductivity.
Key Benefits of GRP Composite Housings
Why are GRP composite housings becoming the preferred choice across industries? Here are some key benefits:
1. Lightweight Strength
One of the primary advantages of GRP composite housings is their lightweight nature. Despite being significantly lighter than metals like steel or aluminum, they offer comparable, if not superior, mechanical strength. This characteristic is particularly beneficial in sectors such as aerospace and automotive, where weight reduction translates directly into enhanced performance and fuel efficiency.
2. Corrosion Resistance
GRP composite housings exhibit remarkable resistance to corrosion, making them ideal for harsh environments such as chemical processing plants, oil and gas fields, and marine applications. They do not corrode or degrade like metals when exposed to corrosive substances, ensuring longevity and reduced maintenance costs.
3. Thermal and Electrical Insulation
Another benefit is the excellent thermal and electrical insulation properties of GRP. In applications where insulation is critical, such as electrical enclosures and housing for sensitive equipment, GRP provides an effective barrier against heat and electricity.
4. Design Flexibility
GRP composite housings can be molded into complex shapes, allowing for innovative designs that traditional materials may not permit. This flexibility facilitates not only aesthetic appeal but also improves functionality and efficiency.
5. Cost-Effectiveness
While the initial investment in GRP composite housings may be higher than traditional materials, the long-term savings on maintenance, replacements, and fuel efficiency contribute to their cost-effectiveness.
Applications of GRP Composite Housings
The versatility of GRP composite housings has led to their widespread application across various industries. Below are some notable sectors utilizing this advanced technology:
1. Telecommunications
In the telecommunications industry, GRP composite housings are used for outdoor cabinets and enclosures that protect sensitive electronic equipment from the elements. Their lightweight and durable nature ensures easy installation while providing secure protection.
2. Marine Industry
The marine industry benefits significantly from the application of GRP composite housings. They are frequently used in boat manufacturing for hulls, decks, and cabins, providing resistance to saltwater and severe weather conditions while decreasing overall weight.
3. Electrical and Electronics
GRP composite housings are widely used for electrical enclosures, switchgear, and other electrical components due to their excellent insulating properties. They provide safety from electrical shocks and ensure operational effectiveness in challenging environments.
4. Aerospace and Automotive
In aerospace and automotive, the need for lightweight and strong materials is critical. GRP composite housings can be found in various applications, from exterior body panels to internal components, contributing to improved fuel efficiency and performance.
5. Infrastructure and Construction
In infrastructure, GRP composite housings are utilized for items such as manhole covers, gratings, and pipe systems. Their corrosion resistance and lightweight properties make them suitable for long-term durability and reduced installation costs.
Innovations in GRP Composite Housing Technology
The advancements in manufacturing processes are continuously enhancing the performance and applications of GRP composite housings. Some of the recent innovations include:
1. Advanced Manufacturing Techniques
Manufacturing processes such as 3D printing and automated fiber placement (AFP) are being utilized to produce bespoke GRP composite housings that meet specific customer requirements with greater efficiency and precision.
2. Sustainability Initiatives
As environmental concerns grow, the industry is looking towards using recycled materials in the production of GRP composites. This not only reduces waste but also enhances the sustainability of products while maintaining performance.
3. Smart Materials Integration
Researchers are exploring the integration of smart materials such as sensors into GRP composite housings. These innovations can lead to self-monitoring systems that alert users to potential failures or environmental impacts.
Future Outlook of GRP Composite Housings
As industries continue to evolve, the demand for lightweight, durable, and versatile materials like GRP composite housings is expected to grow. The ongoing research and development in composite materials will likely lead to even more advanced applications and improved performance characteristics.
Conclusion
The advantages and applications of GRP composite housings are extensive, making them an integral component across various industries. Their lightweight strength, corrosion resistance, design flexibility, and cost-effectiveness underscore why they are increasingly being adopted globally. As innovation in this field continues to advance, the sustainability and efficiency of GRP composites promise to shape the future of manufacturing and design.
In conclusion, if you are looking for a durable, cost-effective solution for your housing needs, consider adopting GRP composite housings in your business practices. Their benefits go beyond the surface, promising not only performance but also longevity in a dynamic industrial environment.